Ethanol-fueled HVOF Technology - The eGun™
The eGun™ is a liquid fuel HVOF torch that utilizes ethanol as its fuel. The eGun™ is capable of operating at combustion chamber pressures up to 13 bar (188 PSI). This is 3 to 5 bar (43 – 73 PSI) greater than conventional kerosene HP-HVOF systems. It has been shown that higher combustion chamber pressure generates higher flame velocity which in turn generates higher particle velocity. Higher particle velocity results in improved coating density and better overall coating integrity. It is also very easy to run at low flame velocity for slow and hot parameters to produce very good bonding (rough) flash coats.
Introduction
When Flame Spray Technologies (FST) began investigating the proposition of developing and introducing a new thermal spray gun (technology) of our own manufacture, we asked ourselves the following question: how can we reduce operational costs and increase application efficiency without compromising coating quality?
To develop our own technology, we analysed the key points of coating formation and particle parameters. We found that spraying “hot and fast” doesn’t necessarily result in a quality coating. The optimal balance between particle kinetic and thermal energy is needed. Of the two, kinetic energy is the more flexible tool. Kinetic energy is proportional to combustion chamber pressure (high pressure = high kinetic energy).
Figure 1: Rendering of the eGun™
After an intensive development program, FST is pleased to announce the eGun™ System together with the eGun™. The eGun™ is a liquid fuel HVOF gun that utilizes ethanol as its fuel. The eGun™ is capable of imparting higher particle velocities due to its ability to achieve higher combustion chamber pressures of up to 13 bar (188 PSI). There are many advantages to using ethanol as compared to kerosene which will be discussed in some detail as we proceed through this document.
The eGun™ System, with the unique High Pressure HP-HVOF eGun™ represents the latest liquid fuel HVOF technology. With this system we are bringing a new and unique coating technology to market. Numerous spray trials have demonstrated that the eGun™ produces coatings of equal or higher quality compared to conventional HVOF or HP-HVOF torches.
Cleaner
Ethanol (C2H5OH) is a low cost non-petroleum based fuel. It is produced globally and easy to obtain. Ethanol is a very consistent fuel providing repeatable and reproducible coatings in contrast to kerosene which consists of a varying mixture of different hydrocarbon chains.
Burning ethanol results in 30% less toxic emissions than kerosene. Ethanol doesn’t have side effects related to ash formation. There is no potential for contamination of a coating by carbon even if fuel-rich mixtures are used.
Using ethanol fuels instead of other alternatives has environment benefits. It is renewable, domestically produced and produces less greenhouse gas emissions than kerosene. The carbon dioxide released when ethanol is burned is balanced by the carbon dioxide captured when the crops are grown to make ethanol. This differs from petroleum, which is made from plants that grew millions of years ago. On a life cycle analysis basis, corn-based ethanol production and use reduces greenhouse gas emissions (GHGs) by up to 52% compared to gasoline production and use. Cellulosic ethanol use could reduce GHGs by as much as 86%.
Figure 2: Bio-ethanol fuel life cycle
Ethanol is a relatively safe fuel and in the event of a fire can be extinguished using water. It is also one of the few fuels that may be used in an indoor table burner or cooking stove. Comparing the safety labelling on the barrels between ethanol and kerosene, there is only one highly flammable sign with ethanol compared to 6 such indications for kerosene.
Since combustion of ethanol does not produce soot the eGun™ System can be operated with neutral, oxygen-rich or fuel-rich parameters. This large operating window provides the opportunity to develop unique coating microstructures using conventional powders. For example, by using radial powder injection in combination with a fuel-rich combustion mixture a unique reducing flight path is created. In effect the eGun™ gives better control over the balance between the kinetic and thermal energy.
The combination of pre-combustion chamber along with an optimized (smaller) combustion chamber provides more efficient combustion resulting in more heat transfer to the powder. By burning a portion of the ethanol in the pre-combustion chamber, heat is provided to the specially designed evaporation cartridge allowing a highly efficient fuel mixture in the combustion chamber. By introducing this multi-stage combustion module concept a significantly smaller main combustion chamber is required. This contributed to the reduction in the overall size and weight of the eGun™.
Figure 3: Comparison of combustion chambers (JP-5220 is a trademark of Praxair)
By reducing the size of the combustion module the energy required for gun cooling has been reduced by as much as 50 to 70% when compared to conventional kerosene processes. By reducing the required cooling capacity, more energy is available to heat the powder particles. This also has the positive effect of reducing coating costs by requiring a smaller less expensive chiller along with lower power consumption. It may even be possible to use your existing plasma cooling unit to cool the eGun™.
Technology
The eGun™ is capable of operating at combustion chamber pressures up to 13 bar (188 PSI). This is 3 to 5 bar (43 – 73 PSI) greater than conventional kerosene HVOF systems. It has been shown that higher combustion chamber pressure generates higher flame velocity which in turn generates higher particle velocity. Higher particle velocity results in improved coating density and better overall coating integrity. It is also very easy to run at low flame velocity for slow and hot parameters to produce very good bonding (rough) flash coats.
Harsh starting explosions during system ignition, common with kerosene guns, is not an issue with the eGun™. Ramping-up the eGun™ System from a very slow idle mode flame to full flow is smooth and efficient.
The eGun™ schematic shows the basic design of the gun. Ethanol and oxygen are injected, mixed and atomized in the pre-chamber and then ignited. The mixture partially burns creating a fully atomized and very combustible fuel oxygen mixture. This mixture enters into the combustion chamber where efficient, stable, clean, uniform and high pressure combustion occurs. The efficient combustion of ethanol allows for low oxygen consumption. In comparison with conventional kerosene processes oxygen consumption is reduced by 30% to 50%. After exiting the combustion chamber the gasses pass through a carefully defined nozzle creating a supersonic flame. At the end of the combustion chamber the powder is radial injected into the barrel. Optimizing powder injection reduces barrel loading in addition to creating optimal powder heating. After injection into the barrel, the powder is uniformly mixed, heated and accelerated to very high speeds.
Figure 4: Schematic cross-sectional sketch of eGun™
By accurately monitoring fuel and oxygen flows, pressures, and cooling water temperatures the combustion process can be precisely controlled. Controlling the condition of the flame also means controlling the coating quality.
Figure 5: Microscopic cross section of an eGun™ sprayed WC-CoCr layer (Amperit 558.059)
- Micro hardness 1314 HV0.3
- Porosity >0.2%
Particle velocity and temperature
The particle velocities for many common powders have been measured when using the eGun System and have been shown to be above the measured speed of other processes. Chrome carbide particles (-45+15 µm) speeds of up to 850 m/s (2788 ft/s) have been measured, while for WC-CoCr (-45+15 µm) speeds of up to 750 m/s (2460 ft/s)have been measured. Metal particles speeds of up to 1000 m/s (3280 ft/s) have also been measured.
The Ethanol HVOF torch has a very wide operating window allowing it to reproduce flame parameters equivalent to the existing HP HVOF systems as well to generate presently unavailable parameters. (Higher Pressure, Fuel Rich, Reducing Atmosphere HVOF Flames)
Positioning the eGun™
Typical liquid fuel parameter comparison
* Combustion Chamber Pressure
** Average Particle Velocity measured by SprayWatch
The eGun can be applied with the following systems:
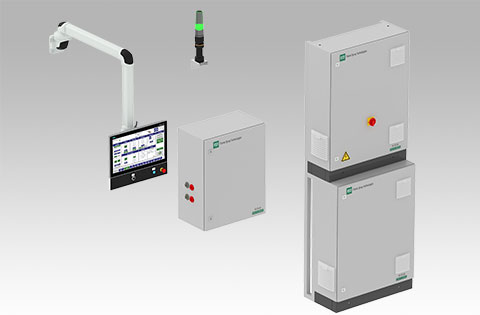
HV-50 HVOF - liquid fuel
The HV-50LF is a stand-alone single process coating system, with mass flow controllers (MFC) for process gases and ES-flow controllers for liquid fuels.
Read more
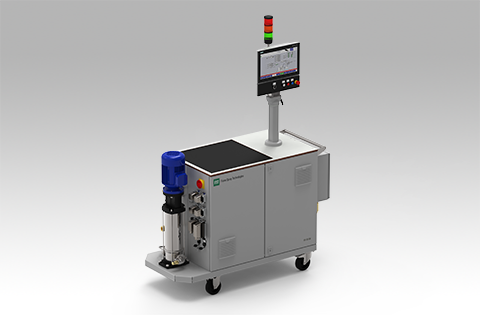
HV-50-LF/M MOBILE - Liquid fuel
The HV-50-LF/M is a mobile stand-alone single process coating system using only state-of-the-art components and technologies.
Read more
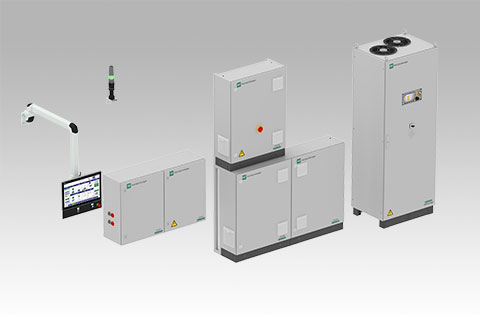
MP-50 - Multi process
The MP-50 makes it possible to perform both HVOF, plasma and combustion spray coatings with one system.
Read moreDownloads
FST Greenbook-2020 - Spare parts section
FST Greenbook-2020 - Thermal spray consumables guide
References
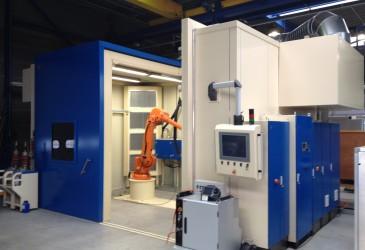
Project TEI 1.0
Robotic Thermal Spray System
MP-X/APS/HVOF
Application/Industry:
Aerospace
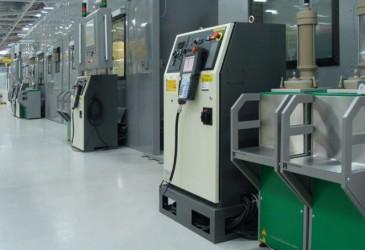
Project Siemens WS
5x Robotic Thermal Spray System
MP-X/APS/HVOF
Application/Industry:
Industrial Gas Turbine
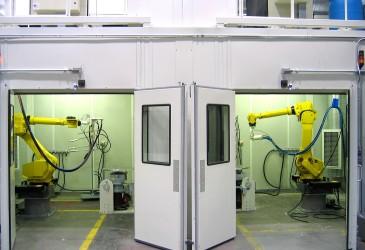
Project Siemens TX
2x Robotic Thermal Spray Systems
MP-X/APS/HVOF
Application/Industry:
Industrial Gas Turbine
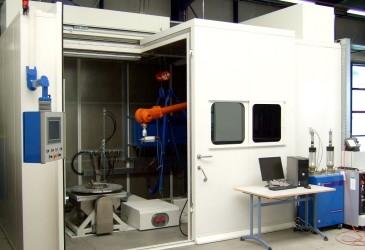
Project Wamar
Robotic Thermal Spray System
MP-X/APS/HVOF
Application/Industry:
Industrial Gas Turbine
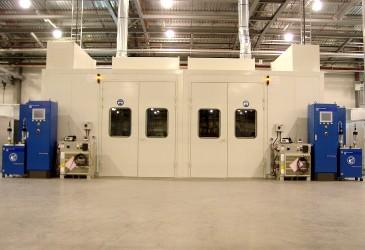
Project Rolls Royce
2x Robotic Thermal Spray System
MP-X/APS/HVOF
Application/Industry:
Aerospace
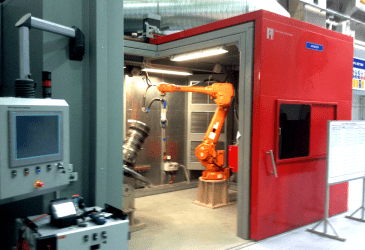
Project Maintenance Partners
Robotic Thermal Spray System
MP-X/APS/HVOF
Application/Industry:
Industrial Gas Turbine
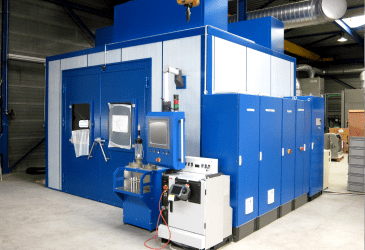
Project MJB
Robotic Thermal Spray System
MP-X/APS/HVOF
Application/Industry:
Industrial Gas Turbine
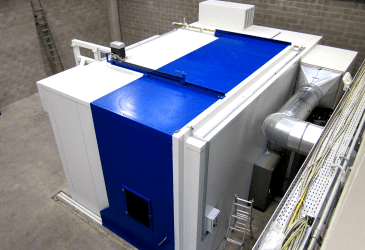
Project Cromostamp
Turn-key Thermal Spray System
MP-50/APS/HVOF
Application/Industry:
General Engineering
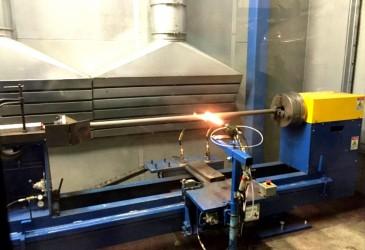
Project Coastal Hydraulics
Turnkey Thermal Spray System
eGun™ System Mobile
Application/Industry:
Hydraulics
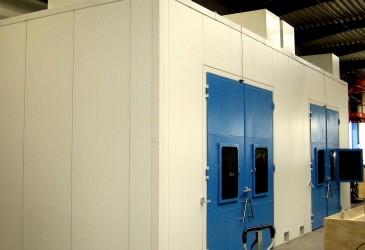
Project RRBS
4x Thermal Spray Systems
Application/Industry:
General Engineering

Project TEI 2.0
2x Robotic Thermal Spray Systems
MP-50 APS/HVOF
Application/Industry:
Aerospace
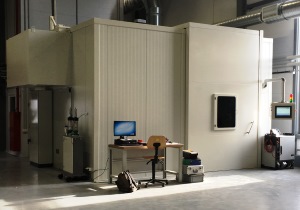
Project Siemens
Robotic Thermal Spray System
MP-50 APS/HVOF
Application/Industry:
Industrial Gas Turbine
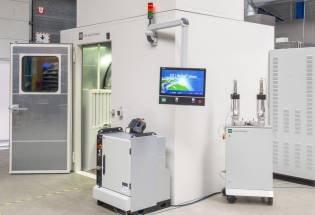
Project Sartori
1x Robotic Thermal Spray System
AP-50 APS
Application/Industry:
Medical Implants
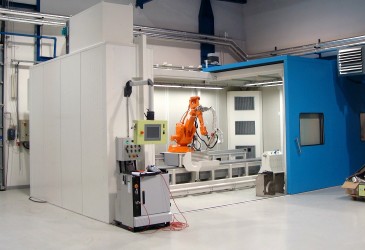
Project Safina
1x Robotic Thermal Spray System
Cold gas system turn-key
Application/Industry:
Precious metals