Cold gas spray systems
In comparison to other thermal spray processes, cold gas spraying offers special advantages, because the spraying material is not fused or melted during the process. The range of coating thickness varies from 0.05mm up to several centimeters.
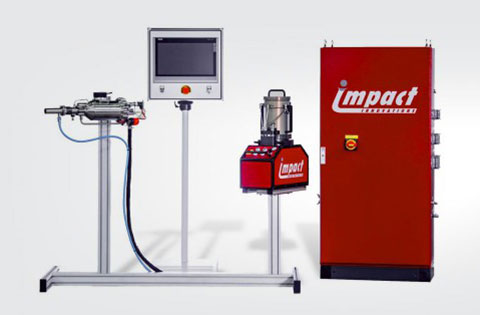
Impact Cold Spray System 5/8
Cold gas spraying offers special advantages, because the spraying material is neither fused nor melted during the process.
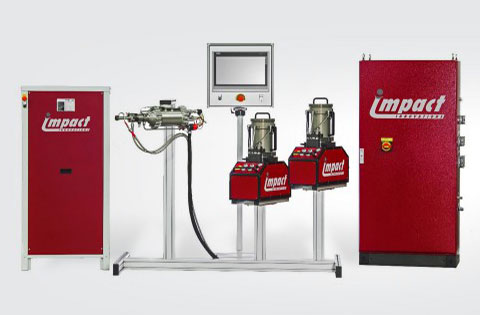
Impact Cold Spray System 5/11
Cold gas spraying offers special advantages, because the spraying material is neither fused nor melted during the process.
Cold gas spray coating process
Cold gas spraying is the most recent method in the field of thermal spraying. It is an emerging coating deposition process where high pressure, low-temperature gas is utilised to accelerate coating material particles to supersonic velocities (400 – 1200 m/s). Upon impact, sufficient energy is generated for a permanent change in shape, known as plastic deformation, and cold welding of the coating and substrate materials occurs.
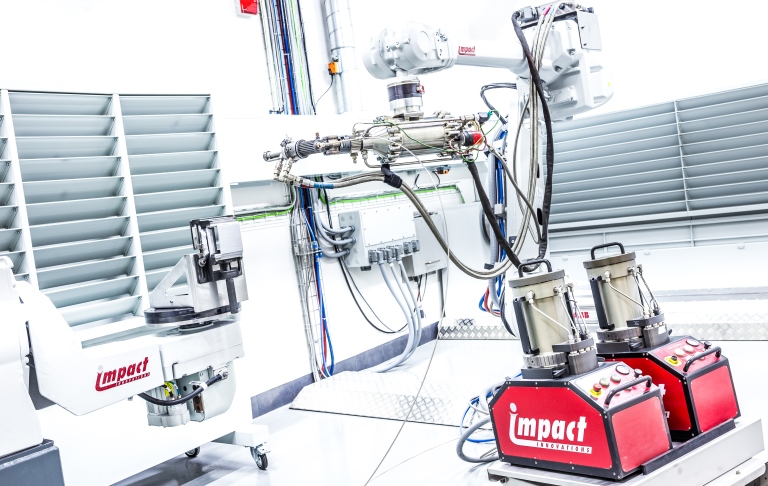
More information about Cold Gas Spray process?
Flame Spray Technologies offer cold spray equipment in partnership with Impact Innovations GmbH. Cold spray can be considered as a new “HVOF” technology where kinetic energy is increased while thermal energy is lowered. With cold spray, it is possible to spray virtually oxide-free coatings. The coating material particles are accelerated in a heated gas stream (600 °C), up to a velocity of >1200m/s. This extremely high particle velocity combined with the low temperature produces a very dense and oxide-free coating. Applications are found in the automotive, corrosion protection and electronics industries.